Was heist DFMEA?
Die Entwurfs-Fehlermöglichkeits- und -einflussanalyse (Design Failure Mode and Effects Analysis / Abkürzung: DFMEA) ist laut Definition ein Prozess, der im Laufe der Produktentwicklung durchgeführt wird. Er dient dazu sicherzustellen, dass die Produkte nicht nur ihre beabsichtigten Funktionen, sondern ebenso die Nutzererwartungen, erfüllen.
Die DFMEA bewertet die Gesamtheit von Produktsystemen und -komponenten, um potenzielle Fehlerarten und -ursachen zu ermitteln. Sie wird deshalb als Design-FMEA (im Gegensatz zur „einfachen“ FMEA) bezeichnet, da sie zusätzlich Handlungsempfehlungen zur Beseitigung oder Minimierung möglicher Auswirkungen von Entwurfsfehlern auf den Anwender eines Produkts gibt.
Die Design Failure Mode and Effects Analysis ist besonders in der Fertigungsindustrie und im Maschinenbau von Bedeutung, in welcher Risikominderung und Fehlervermeidung von grundlegender Bedeutung sind. Die Durchführung einer effektiven FMEA-Analyse ermöglicht es Entwicklungsteams, ihren Entwurf besser zu verstehen und seine Sicherheit zu verbessern, um am Ende ein qualitativ hochwertiges Produkt zu entwickeln.
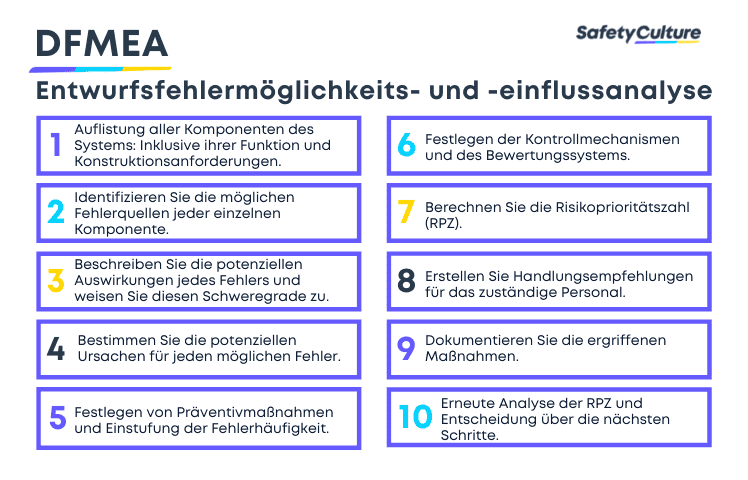
Design Failure Mode and Effects Analysis (DFMEA) Methode | Wie Sie den DFMEA-Prozess konkret in 10 Schritten durchführen!
Was ist der Unterschied zwischen DFMEA und FMEA?
Der Hauptunterschied zwischen DFMEA und FMEA besteht darin, dass sich Erstere speziell auf die Identifizierung von Fehlermöglichkeiten, -ursachen und -auswirkungen eines Produktdesigns konzentriert. Während die FMEA allgemeine Leitlinien bietet, welche auf einen Prozess oder eine Dienstleistung angewendet werden können.
Die Entwurfsfehlermöglichkeits- und -einflussanalyse wird häufig mit der Prozessfehlermöglichkeits- und -einflussanalyse (PFMEA) gleichgesetzt. Sie unterscheiden sich jedoch darin, in welcher Phase des Produktentwicklungsprozesses sie jeweils durchgeführt werden.
Warum ist eine DFMEA wichtig?
Die DFMEA ist wichtig, weil mit ihr potenzielle Konstruktionsfehler bereits zu Beginn erkannt und korrigiert werden. Das senkt in weiterer Folge die Entwicklungszeit und -kosten des Endprodukts. Der DFMEA-Prozess führt ebenso dazu, dass ein robusterer Entwurf mit klar definierten Anforderungen erstellt wird. Falls eine Komponente zum Beispiel keine nützliche Funktion hat, sollte sie nicht Teil des Entwurfs sein.
Wer sollte an einer DFMEA teilnehmen?
Ein typisches DFMEA-Team besteht aus 4 bis 6 Mitarbeitern, die den Entwurf, seine Anforderungen und Überlegungen zur Herstellbarkeit genau verstehen. In der Regel leitet ein Produktentwicklungsingenieur dieses funktionsübergreifende Team. Die weiteren Mitglieder sind Ingenieure für Material, Testanalyse und Produktqualität. Auch Vertreter anderer Abteilungen wie Produktion, Service und Logistik können in das Verfahren mit einbezogen werden.
Wann sollte eine DFMEA durchgeführt werden?
Die erste Entwurfsfehlermöglichkeits- und -einflussanalyse sollte abgeschlossen sein, bevor die Zeichnungen für Fertigung und Verfahrenstechnik freigegeben werden. So bleibt genügend Zeit, um den Entwurf zu bewerten, bevor der Prozess zur Herstellung des Produkts in die Wege geleitet wird. Ein weiterer Fall, in dem eine DFMEA durchgeführt werden sollte, ist, wenn der aktuelle Entwurf geändert wird – entweder als Folge eines früheren Fehlers oder zur weiteren Produktverbesserung.
Wie Sie den DFMEA-Prozess konkret in 10 Schritten durchführen
In der Praxis hängen die Schritte für die DFMEA-Implementierung von bestimmten Unternehmensprotokollen ab. Sie variieren damit zwischen verschiedenen Sektoren wie der Luft- und Raumfahrt, der Schifffahrt und der Automobilindustrie. Auch wenn der Prozess aufgrund seines Umfangs zunächst eventuell einschüchternd wirkt, ist er als strukturierter und logischer Ansatz für die Analyse äußerst wertvoll. Um Ihnen den Einstieg zu erleichtern, haben wir Ihnen im Folgenden ein Beispiel für die Durchführung eines 10-stufigen DFMEA-Prozesses erstellt:
Schritt 1: Auflistung aller Komponenten des Systems: Inklusive ihrer Funktion und Konstruktionsanforderungen.
Eine der einfachsten Möglichkeiten, dies zu erreichen, besteht darin, den Produktentwurf zuerst in einzelne Komponenten (mit eigener Funktion) zu zerlegen. Und diese danach in einem Entwurfs- und Funktionsbaum zu organisieren. Diese Visualisierungen helfen Ihnen dabei die Beziehung zwischen dem Gesamtdesign, den einzelnen Komponenten und deren Funktionen zu veranschaulichen.
Beispiel: Das Sitzsystem eines einfachen Stuhls könnte aus dem Sitz selbst (um das Gewicht des Benutzers zu tragen), Schürzen (um die Kanten des Sitzes zu verstärken), Eckblöcken (um die Schürzen an den Beinen zu befestigen) und Befestigungselemente (um die Eckblöcke an den Schürzen zu halten) bestehen.
Schritt 2: Identifizieren Sie die möglichen Fehlerquellen jeder einzelnen Komponente.
Ein Fehler ist ein Zustand, in dem ein Produkt die Bedürfnisse der Nutzer und/oder die beabsichtigten Funktionen nicht erfüllt. Da die Funktion eines Sitzsystems darin besteht, das Gewicht des Benutzers zu tragen, besteht eine der möglichen Fehlerarten darin, dass der Sitz bricht.
Schritt 3: Beschreiben Sie die potenziellen Auswirkungen jedes Fehlers und weisen Sie diesen Schweregrade zu.
Eine Fehlerauswirkung ist das direkte Ergebnis eines aufgetretenen Fehlers. Zu den möglichen Folgen eines gebrochenen Sitzes gehören die Freilegung scharfer Kanten, der Zusammenbruch des Stuhls und die Verletzung des Benutzers. Auf der Grundlage festgelegter Kriterien sollte diesen Folgen ein Schweregrad basierend auf den möglichen Auswirkungen auf den Benutzer zugewiesen werden.
Beispiel: Die Einstufung des Schweregrads einer Fehlerauswirkung mit 1 bedeutet, dass sie minimale Auswirkungen auf den Benutzer hat. Eine Auswirkung mit einem Schweregrad von 10 bedeutet hingegen, dass der Konstruktionsfehler die Sicherheit des Benutzers oder die Einhaltung von Vorschriften deutlich beeinträchtigt.
Schritt 4: Bestimmen Sie die potenziellen Ursachen für jeden möglichen Fehler.
Nach der Festlegung eines Schweregrads sollten Sie des Weiteren die Ursache(n) für jeden möglichen Fehler untersuchen. In einigen Fällen liegt die Ursache eines Konstruktionsfehlers in Funktionsfehlern von Bauteilen, wie z. B. zu dünnen Sitzen, schwachen Schürzen, abgescherten Eckblöcken und losen Befestigungselementen, um bei der Fehlerannahme „Sitzbruch“ zu bleiben.
Schritt 5: Festlegen von Präventivmaßnahmen und Einstufung der Fehlerhäufigkeit.
DFMEA-Präventionskontrollen sind spezifische Maßnahmen, die ergriffen werden, um die Ursachen von Fehlern zu verhindern. Denken Sie daran, dass es sich dabei um laufende Präventionsmaßnahmen handelt. Je nachdem, wie wahrscheinlich es ist, dass eine Fehlerursache auch bei bereits ergriffenen Vorbeugungsmaßnahmen bestehen bleibt, sollte eine Ereignisbewertung vorgenommen werden.
Dabei bedeutet 1, dass es sehr unwahrscheinlich oder fast unmöglich ist, dass die Ursache trotz laufender Präventionskontrollen auftritt. Während 10 wiederum bedeutet, dass es sehr wahrscheinlich oder fast sicher ist, dass die Ursache immer noch vorhanden ist und in weiterer Folge zum Auftreten von Produktproblemen führt.
Schritt 6: Festlegen der Kontrollmechanismen und des Bewertungssystems.
DFMEA-Erkennungskontrollen sind Verfahren, die implementiert werden, um die Erkennung von Fehlerursachen zu verbessern. Und zwar bevor die Konstruktionszeichnungen und Spezifikationen fertiggestellt werden. Zu diesen Aufdeckungsaktivitäten gehören beispielsweise Sichtkontrollen, Haltbarkeitstests und Kundenrezensionen.
Unabhängig von den Methoden sollte eine Bewertung von diesen auf der Grundlage der Wahrscheinlichkeit vorgenommen werden, dass diese Maßnahmen tatsächlich Fehlerursachen aufdecken. Die Bewertung einer Kontrollmethode mit 1 bedeutet, dass sie eine Fehlerursache mit Sicherheit aufdecken kann. Während eine Bewertung von 10 bedeutet, dass eine Fehlerursache trotz laufender Kontrollen unentdeckt bleiben kann.
Schritt 7: Berechnen Sie die Risikoprioritätszahl (RPZ).
In der DFMEA wird eine Risikoprioritätsnummer in erster Linie verwendet, um den Teams bei der Priorisierung der zu bearbeitenden Fehlerursachen zu helfen. Ermitteln Sie die RPZ durch Multiplikation aller DFMEA-Bewertungen: Schweregrad, Auftreten und Entdeckung. Es ist wichtig zu beachten, dass die DFMEA-Bewertung relativ zu den anderen Zahlen funktioniert. Angenommen, 3 verschiedene Fehlermodi haben eine RPZ von 60, 120 bzw. 30, dann sollte der zweite Fehlermodus (RPZ von 120) vorrangig behandelt werden. Ein im Voraus festgelegter RPZ-Schwellenwert (z. B. 100 und darüber) kann den Entscheidungsprozess, welche Fehlermodi zuerst in Angriff genommen werden sollen, weiter optimieren.
Schritt 8: Erstellen Sie Handlungsempfehlungen für das zuständige Personal.
Bei der Identifizierung von Fehlermodi mit RPZs, die den Grenzwert überschreiten, sollten dem zuständigen Personal empfohlene Maßnahmen inklusive Zielterminen für die Behebung zugewiesen werden. Bei der Festlegung der zu ergreifenden Maßnahmen ist zu überlegen, wie die Schwere der Auswirkungen von Fehlern verringert werden kann oder ob neue Präventiv- und Aufdeckungsmaßnahmen die Häufigkeit des Auftretens und die Entdeckungsrate verringern können.
Schritt 9: Dokumentieren Sie die ergriffenen Maßnahmen.
Auch wenn die Entwurfsfehlermöglichkeits- und -einflussanalyse systematisch fundierte Empfehlungen liefern kann, kann es dennoch sein, dass die Dinge danach immer noch nicht wie geplant laufen. Welche Maßnahmen auch immer ergriffen werden, sie sollten deshalb immer mit dem tatsächlichen Abschlussdatum dokumentiert werden. Das DFMEA-Formular sollte ebenfalls entsprechend aktualisiert werden, um das DFMEA-Teams bestmöglich bei der Verfolgung und Überwachung ihrer Fortschritte zu unterstützen.
Schritt 10: Erneute Analyse der RPZ und Entscheidung über die nächsten Schritte.
Schließlich sollten die Risikoprioritätszahlen der Ziel-Fehlerursachen neu berechnet werden, da ja bereits Maßnahmen zur Verbesserung des Entwurfs ergriffen wurden. Wenn das Team feststellt, dass durch die vorgenommenen Änderungen alle Risiken beseitigt wurden, kann der Produktentwurf im Produktentwicklungsprozess fortgesetzt werden.
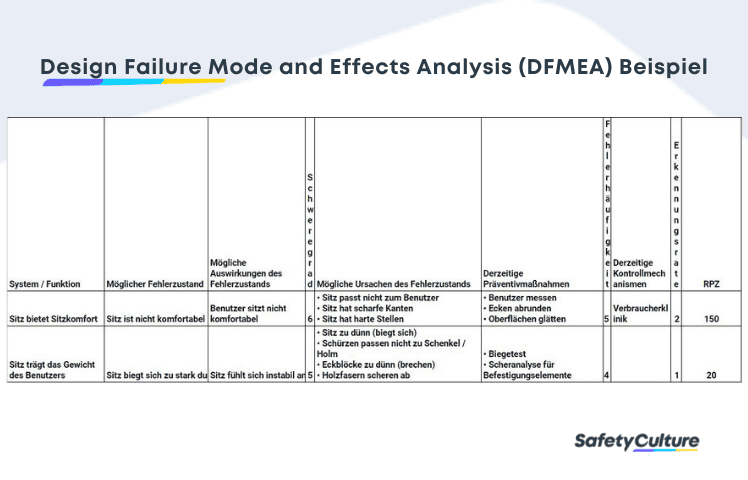
DFMEA-Risikoanalyse: Beispiel für die optimale Vorgehensweise (Tabelle) | Quelle
DFMEA-Fehleranalyse und -Aktionspläne
Das richtige Durchlaufen des DFMEA-Prozesses ist eine Disziplin, die Geduld und Übung erfordert. Es mag Zeiten geben, in denen es sich so anfühlt, als würde Ihr Team zwei Schritte vor und einen zurück machen. In dem gleichen Maße, in dem die Design-FMEA die Komplexität des zu analysierenden Produkts aufdeckt, beginnen die Sorgen zu wachsen. Wir haben 3 der häufigsten Fehler zusammengestellt, die DFMEA-Teams begehen. Und wie sie diese vermeiden:
- Übersehen von nicht funktionsbezogenen Entwurfsanforderungen: Während die Fehlermodi des Entwurfs oft mit den Systemfunktionen in Verbindung gebracht werden, sollten auch andere Anforderungen berücksichtigt werden. Zum Beispiel: Es gibt mindestens 14 Arten von Konstruktionsanforderungen für allgemeine Produkte, wie Kostenziele, Ästhetik, Kapazität, Ein-/Ausgänge und ökologische, gesetzliche oder lizenzrechtliche Überlegungen.
- Hinzufügen von Fehlerursachen, welche nicht die eigentlich zugrundeliegende Ursache darstellen: Es mag hilfreich sein, alle möglichen Ursachen für Fehler aufzuzählen. Den größten Nutzen aus einer DFMEA ziehen Sie jedoch, wenn Sie sich auf die Behebung der Hauptursachen konzentrieren. Angemessene Präventionskontrollen können nur dann festgelegt werden, wenn die Hauptursachen von Produktfehlern ermittelt wurden. Sie können verschiedene Techniken zur Analyse von Fehlerursachen anwenden, um sicherzustellen, dass diese gefunden und behoben werden.
- Standardisierung der laufenden sowie geplanten vorbeugenden Kontrollen: Eine Kontrollmaßnahme ist in der Regel viel einfacher zu definieren und einzurichten, da sie reaktiv ist – sie wird durchgeführt, um Fehler zu erkennen. Im Gegensatz dazu muss eine Präventivmaßnahme viel spezifischer sein, da sie als proaktiver Ansatz zur Fehlervermeidung unter ungünstigeren Bedingungen zur Anwendung kommt. Zum Beispiel: Im Folgenden sind einige DFMEA-Kontrollmechanismen – sowohl zur Prävention als auch zur Entdeckung von Fehlern – aufgeführt:
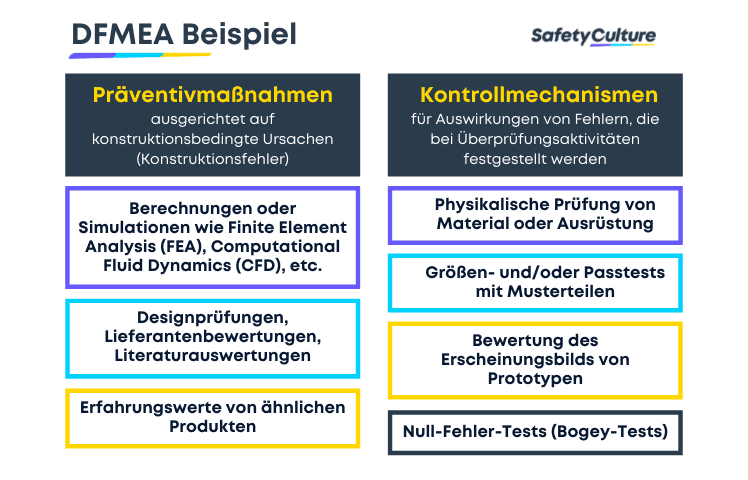
DFMEA-Beispiel: Vorbeugende und fortlaufende Kontrollen